Quando la fabbrica è intelligente e perché
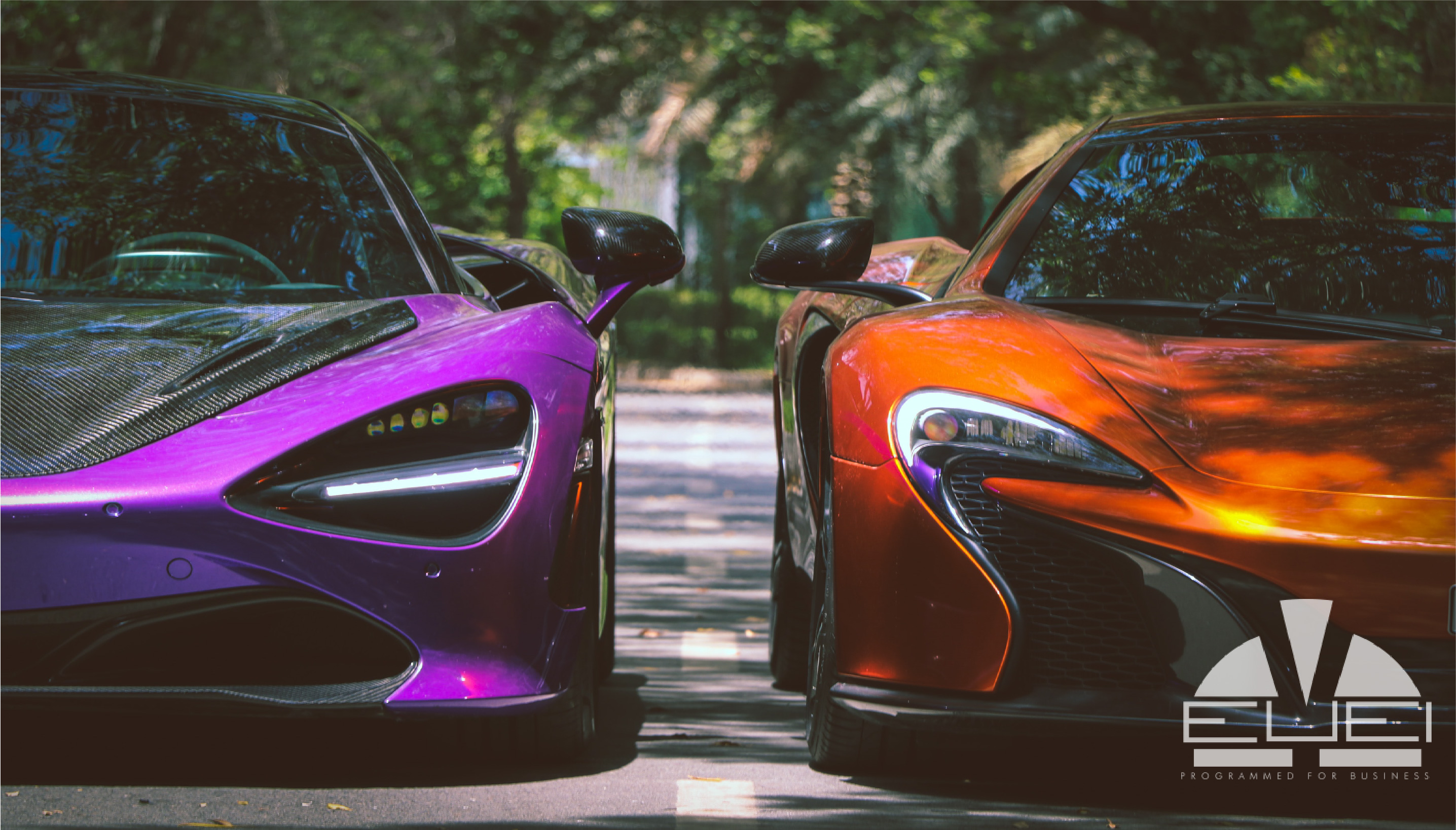
Manca solo un Gran Premio alla fine del campionato F1 2020: Abu Dhabi che inizia oggi.
Il tempo è un fattore determinante, soprattutto quando si parla di realizzare un pezzo di ricambio di un motore di Formula 1, da rifare completamente o solo in parte, poco importa, è essenziale che il pezzo venga prodotto e spedito in tempo per essere montato nel motore per il prossimo Gran Premio. Fin qui, niente di nuovo.
Mettiamoci ora dalla parte di chi deve produrre quel pezzo, adesso, durante questa emergenza sanitaria. L’esigenza di controllare da remoto la produzione di un componente di un motore, monitorare lo stato di operatività della macchina che lo sta realizzando ed essere allertati per un’interruzione o un guasto e capirne i motivi è oggi più che mai essenziale.
Ora spostiamo la nostra attenzione sui motoriduttori senza i quali potremmo avere “qualche problema”: non potremmo sollevare, abbassare e movimentare merci di qualsiasi genere in qualunque impianto. Nel settore automobilistico i motoriduttori sono essenziali alla produzione. Sono fondamentali in molti comparti.
Pensiamo adesso a quell’azienda che li produce, anche in questo caso raccogliere ed interpretare i dati da una serie di macchine eterogenee che compongono le isole di produzione è importante per avere un dettaglio analitico e in tempo reale di eventi come i fermi macchina e le loro cause. Tutto questo con l’invio al cloud dei dati per la manutenzione predittiva, ottenendo una reportistica unica con il riepilogo delle cause dei fermi integrata con il gestionale di fabbrica (MES).
Integrare diverse fonti dati all’interno di un unico sistema porta a risolvere il problema di causalizzazione dei fermi, migliorando tempestività, efficacia e precisione nell’individuazione della prima macchina responsabile dell’innesco del fermo.
Nell’industria manifatturiera è imperativo conoscere lo stato operativo e di produzione in totale visibilità; ovunque e sempre, visualizzandolo con qualsiasi dispositivo per aiutare a eliminare i tempi di fermo e ad aumentare la produttività. Non solo, è cruciale poter contare su un servizio che permetta di conoscere in tempo reale la disponibilità di una macchina utensile per pianificare le produzioni successive; così come avere sotto controllo i dati relativi all’energia e alle materie prime utilizzate.
Questo è possibile grazie all’adozione di servizi Industria 4.0 che sono in grado di raccogliere dati e lavorare in sicurezza, garantendo così anche il distanziamento e gestendo la produzione in remoto senza un presidio locale.
Le piattaforme di monitoraggio, basate su IoT e Industrial IoT, sono le fondamenta della fabbrica intelligente e 4.0 che unisce la convergenza tra i sistemi che gestiscono le informazioni, (Information Technology), e i sistemi che gestiscono la produzione industriale, (Operational Technology) che oggi devono lavorare insieme e rappresentano già uno standard operativo.
Un sistema di monitoraggio in grado quindi di ridurre i costi di produzione, garantire una flessibilità operativa che deve affrontare una domanda fluttuante. Un software capace di portare innovazione e di migliorare la qualità dei prodotti, in grado anche di fornire un servizio al consumatore finale.
Tutto questo si concretizza con Production Sentinel, il servizio di monitoraggio centralizzato per l’Industria 4.0 in grado di rilevare, anche in remoto e attraverso qualsiasi dispositivo mobile, lo stato operativo non solo delle macchine utensili ma anche di altri tipi di dispositivi, i relativi parametri produttivi, la resa e le cause di fermo in tempo reale.
Production Sentinel semplifica l’automazione industriale, migliora le condizioni di lavoro, la produzione e la sua qualità.
Il servizio controlla lo stato operativo ed estrae le informazioni di qualsiasi dispositivo o macchina trasformandole in dati utili e di facile comprensione per potenziare l’efficienza produttiva.
Per una maggiore sinergia tra produzione e manutenzione, è possibile gestire le manutenzioni programmate, automatiche, di emergenza o semplicemente censire gli interventi rilevati dagli operatori, tutto con la possibilità di avere il sistema di raccolta dati integrato con il ciclo di vita delle manutenzioni.
Le aziende citate sono Meccanica GN e Bonfiglioli che hanno adottato Production Sentinel.